O encaixe Quatro impresso em 3D utiliza o Freeform para oferecer uma personalização sem precedentes
Existem 2,7 milhões de americanos vivendo com perda de membros, número que deve quase dobrar até 2050.* Para aqueles com amputação de membros inferiores, recuperar a mobilidade depende de uma prótese que funcione adequadamente e tenha um bom ajuste. Esses dois fatores estão muito interligados, pois um ajuste inadequado pode prejudicar muito a função e o conforto.
Nada disso é mais aparente do que no encaixe protético, a interface entre o membro residual e a prótese. Esses encaixes são tradicionalmente feitos com um molde de gesso que é personalizado para o usuário individual e, em seguida, laminado com carbono e resina. Após múltiplas adaptações, o encaixe final geralmente é feito de fibra de carbono, fibra de vidro ou nylon.
Aqui está o problema: mesmo o encaixe mais precisamente personalizado eventualmente se ajustará mal porque o membro residual não é estático. Não apenas muda de forma e volume durante os primeiros 12 a 18 meses após a cirurgia inicial, mas seu volume continua a flutuar em até 11% ou 12% diariamente. Isso pode levar a encaixes que não se ajustam bem, causam muita pressão e desconforto e, em última análise, tornam muito difícil controlar a prótese.
Entra a Quorum Prosthetics, uma empresa sediada no Colorado por trás do Quatro, um encaixe impresso em 3D com um design patenteado que permite aos usuários alterar o volume e a compressão do encaixe com rolos ajustáveis e células de conforto intercambiáveis que se combinam para proporcionar um melhor ajuste geral e maior conforto.
O Freeform, desenvolvido pela Oqton, é o software que permitiu à Quorum Prosthetics dar vida à ideia.
O CEO da Quorum Prosthetics, Joe Johnson, tem experiência em primeira mão da diferença que esse design faz. Ele usa um encaixe Quatro há mais de três anos.
"É muito mais seguro usar uma prótese que tenha essas células integradas porque consigo sentir onde está meu pé no espaço", diz ele. "O Quatro usa forças opostas que transferem compressão para o encaixe e isso leva a uma melhor propriocepção, que é o seu sentido de posição e movimento do membro. Ele também proporciona um ajuste melhor e mais firme para o usuário. Eles podem controlar o ajuste com microajustes no mostrador."
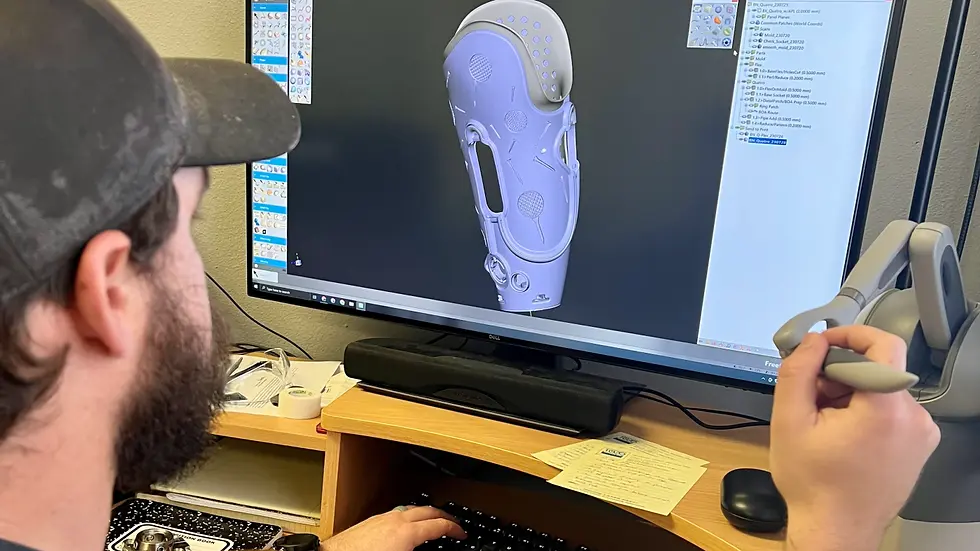
A Quorum Prosthetics utiliza o Freeform para projetar seu encaixe patenteado impresso em 3D, o Quatro.
O grau de ajuste do encaixe Quatro é uma grande razão para o seu sucesso. Os encaixes convencionais são fabricados com uma faixa de precisão de aproximadamente 3 mm. Mas o Quatro tem uma faixa de precisão de menos de um milímetro.
"É muito mais preciso", diz Johnson. "Isso é importante. Quando fazemos o reajuste, podemos reproduzir exatamente isso no interior do encaixe se a pessoa tiver perdido volume desde o ajuste anterior, o que quase sempre acontece. Anteriormente, você não poderia fazer isso. Ou, se pudesse, simplesmente não era muito preciso."
Aumentando a precisão com a tecnologia háptica
A Quorum começou a usar o Freeform quase quatro anos atrás para lançar o Quatro no mercado.
"Tínhamos uma patente para o encaixe Quatro com uma exigência de design muito específica e o Freeform atendeu perfeitamente à necessidade", diz Johnson. "Basicamente, fabricamos encaixes personalizados para cada paciente, então cada forma parece muito diferente. Mas o layout das linhas de ajuste e todo o sistema Quatro foi padronizado no Freeform para tornar o processo de design rápido e fácil."
O processo começa com um encaixe diagnóstico feito por um profissional clínico, que a equipe da Quorum traz para o ambiente de design digital do Freeform por meio de digitalização 3D de alta fidelidade. Em seguida, o designer da Quorum, Sean McClure, organiza a placa base, as carcaças e outros componentes criados por CAD dentro do espaço do molde.
"Aqui é onde a maior precisão realmente entra em jogo", diz McClure. "Tradicionalmente, você poderia esperar estar dentro de um oitavo de polegada. Com o Freeform, podemos ser muito mais precisos."
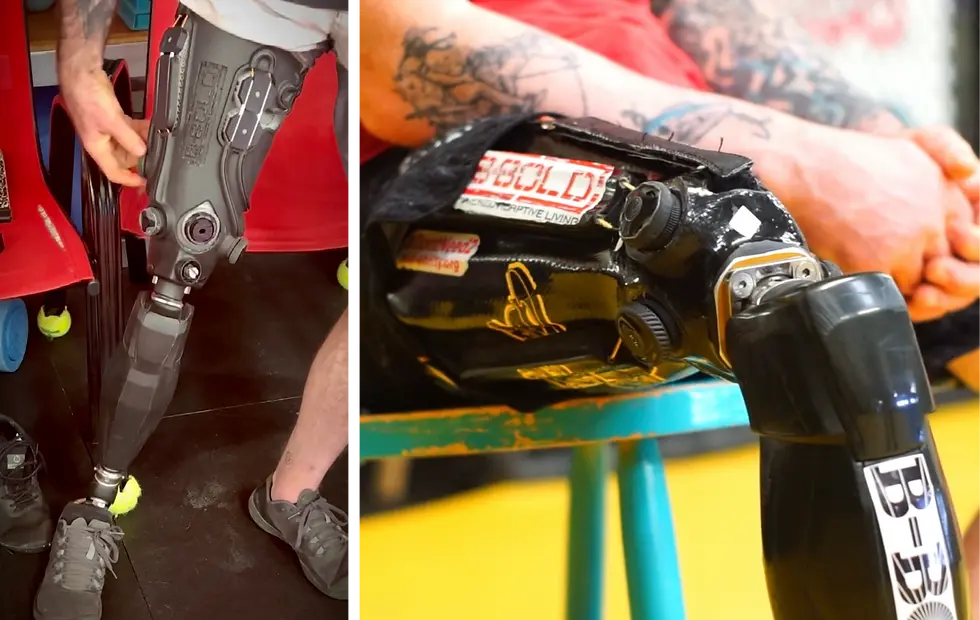
O Quatro utiliza forças opostas que transferem compressão para dentro do encaixe, o que resulta em uma melhor propriocepção, ou seja, o sentido da posição e movimento do membro.
Com os componentes no lugar, as modificações no molde começam em um modelo de argila digital. O Freeform inclui uma ampla gama de ferramentas para esculpir e moldar argila, incluindo lâminas, cortadores de faca e raspadores, todos os quais fornecem feedback háptico. Em seguida, McClure traça a linha do rebordo, faz o encaixe base e prossegue com o design das tecnologias patenteadas do Quatro.
"A tecnologia háptica dentro do Freeform nos permite criar essas curvas muito controladas, o que nos permite incorporar recursos de design padronizados dentro de uma forma totalmente personalizada", diz McClure. "De forma alguma é um modelo. Nosso objetivo principal é fazer um encaixe que se adapte a uma pessoa específica e funcione da maneira que ela precisa."
Neste ponto do processo, McClure combina o modelo sólido original, o modelo de argila e um modelo de malha para chegar a um design final pronto para impressão 3D com uma Impressora HP 4200 MultiJet Fusion. O último passo do processo é o polimento a vapor para obter a qualidade de superfície correta.
Impulsionando a eficiência com impressão 3D
Usando uma abordagem mais tradicional, criar esse tipo de design de encaixe levaria até 12 horas. Com o Freeform, a equipe da Quorum pode finalizar um design em quatro a seis horas, embora alguns tenham sido feitos em tão pouco quanto três. Quando quatro encaixes estão prontos para ir, todos podem ser impressos em 3D simultaneamente para um impulso dramático na eficiência.
"Esperamos até que tenhamos quatro encaixes prontos para imprimir para maximizar a capacidade da nossa impressora", diz Johnson. "O tempo total de fabricação de ponta a ponta é normalmente de uma semana, mas já fizemos em três dias em alguns casos. E muito disso é impressão, resfriamento e pós-processamento. Juntos, Freeform e impressão 3D nos permitem reduzir pela metade nosso tempo de produção."
Johnson também observa que um benefício secundário da impressão 3D é que eles podem ser executados sem supervisão durante a noite, o que não apenas melhora a eficiência geral, mas ajuda a evitar a necessidade de contratar e reter operadores de máquinas durante a escassez de mão de obra.
"A mão de obra qualificada é um dos maiores centros de custo em qualquer empresa de fabricação agora", diz ele. "E está ficando cada vez mais caro. Nossa impressora 3D só precisa de alguma manutenção de tempos em tempos, e ela pode entregar quatro encaixes no mesmo tempo que um técnico tradicional leva para fazer apenas um."

De acordo com o CEO da Quorum Prosthetics, Joe Johnson, o Freeform continua sendo essencial para o trabalho deles.
Expandindo o acesso, mudando vidas
Atualmente, a Quorum é uma empresa em rápido crescimento com uma forte presença na área local do Colorado. Apesar de sua relativa juventude na indústria altamente competitiva de dispositivos médicos, a Quorum está aumentando seu alcance puramente por meio de boca a boca e mídias sociais.
"Normalmente são os pacientes que nos procuram diretamente", diz Johnson. "Os pacientes protéticos tendem a ser mais familiarizados com a tecnologia do que a pessoa média. Eles fazem pesquisas extensas e nos encontram por meio de várias plataformas. Até mesmo tivemos alguns pedidos feitos pelo TikTok."
Infelizmente, o principal motivador neste cenário é a qualidade relativamente baixa do encaixe de fibra de carbono médio, que nem sempre proporciona uma experiência confortável de forma consistente.
"Eu adoraria que todo amputado tivesse acesso ao encaixe Quatro", diz Johnson. "Porque isso mudou minha vida. Os pacientes com quem trabalhamos ficam extasiados quando recebem seus encaixes. Eles gostam de ter mais controle sobre sua prótese. Eles se sentem parte de todo o processo. Eles até podem adicionar um logotipo ou padrão especial ao seu encaixe."
O Freeform continua sendo essencial para o trabalho que a Quorum Prosthetics realiza, tanto em termos de funcionalidade quanto na eficiência que traz ao processo, segundo Johnson.
"Temos um slogan na porta de nossa instalação que diz: 'Aqui é onde as ideias se tornam realidade'", diz ele. "E isso é realmente por causa do Freeform. Sem os componentes e a háptica do software Freeform, não haveria como realizarmos o que fazemos na velocidade que aspiramos."

Comments